Shutdown & Turnaround Success: Are You Set Up for a Smooth Transition?
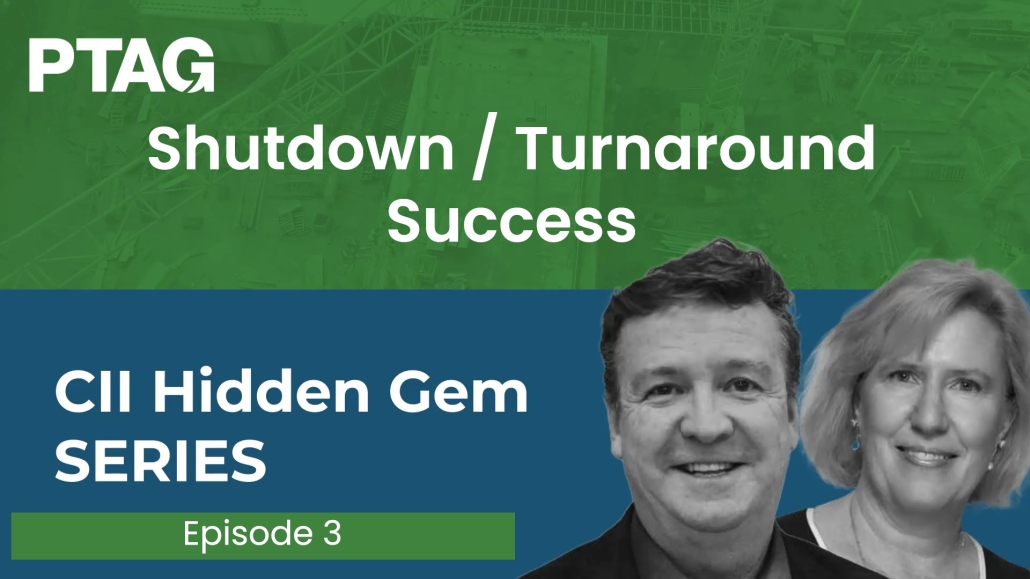
Planned shutdowns and turnarounds are critical milestones in industrial operations. When executed well, they optimize performance, minimize downtime, and ensure long-term reliability. But without proper planning, they can lead to unnecessary delays, cost overruns, and operational inefficiencies.
The key question is:
Data-Is your team truly prepared for the next shutdown, or are there gaps in planning that could cause setbacks? Driven PMOs: Not Your Average Office
That’s exactly what Deborah DeGezelle and Mike Davidson explored in the CII Hidden Gems III: Shutdown & Turnaround Success webinar. Drawing from Construction Industry Institute (CII) Research Team 242, they shared valuable insights and tools to help teams enhance readiness, improve coordination, and execute shutdowns with confidence.
The Challenge: Why Some Shutdowns Struggle to Stay on Track
Shutdowns and turnarounds are fast-paced, high-pressure events with many moving parts. While they’re necessary for asset integrity and performance, they come with common challenges:
• Tight schedules – Every extra day offline impacts production and revenue.
• Scope expansion – Unplanned work can strain resources.
• Stakeholder coordination – Multiple teams must align on execution plans.
• Readiness gaps – If teams aren’t fully prepared, inefficiencies arise.
• Lack of data-driven decision-making – Without structured planning tools, teams often rely on assumptions rather than measurable insights.
Key Data on Shutdown Performance
• 60% of shutdowns and turnarounds experience cost or schedule deviations.
• Projects with structured planning tools achieve greater predictability and cost efficiency.
• Organizations using CII’s STAR (Shutdown Turnaround Alignment Review) tool report improved coordination and risk management.
A Proactive Approach: The STAR Tool
One of the most valuable takeaways from the webinar was the STAR Tool (Shutdown Turnaround Alignment Review)—a structured readiness assessment that helps teams proactively identify potential gaps and align on key priorities.
How the STAR Tool Strengthens STO Planning
- Evaluates readiness across key areas, including permitting, procurement, commissioning, and startup.
- Identifies potential challenges before they impact execution.
- Generates action items to enhance preparation and efficiency.
- Facilitates alignment between operations, maintenance, and project teams.
- Supports data-driven decision-making for more predictable outcomes.
Mike Davidson shared real-world insights from his work with Ontario Power Generation (OPG), where structured planning tools like STAR and PDRI helped transform shutdown execution from reactive to proactive, resulting in improved schedule adherence and cost control.
Key Takeaway
Successful turnarounds don’t just happen—they are built through structured planning and proactive collaboration.
Hidden Gems to Take Home
- Tools that Wow: From the BIPP (Best Productivity Practice Implementation Index) to the PDRI (Project Definition Rating Index), CII’s treasure chest is filled with tools to make your life easier and your projects smarter.
- The Case for Continuous Improvement: Lessons learned aren’t just an end-of-project afterthought. With tools like the STAR (Shutdown Turnaround Alignment Review), you’re equipped for real-time course corrections.
- People Make the Difference: A strong portfolio manager is your ace. RT303 even maps out the skills and authority they need, down to a job description. Now that’s planning.
Strategies for a More Effective Shutdown & Turnaround
- Start Early. The best turnarounds begin long before execution day.
- Leverage Proven Tools. STAR, PDRI, and PCI provide data-driven insights for better planning.
- Align Stakeholders. Coordination between operations, maintenance, construction, and procurement is key.
- Manage Scope Effectively. A structured approach helps control changes and minimize surprises.
- Take a Risk-Based Approach. Identifying risks early leads to better contingency planning.
Bonus Tip
The STAR Tool helps teams assess readiness objectively—providing a clear picture of where preparation stands and where additional focus is needed.
Common Pitfalls & How to Avoid Them
While every shutdown is unique, there are common challenges that can be mitigated with the right approach:
- Ensure readiness is assessed objectively. A structured evaluation helps prevent overly optimistic assumptions.
- Engage key stakeholders in planning. Cross-functional alignment ensures all aspects are accounted for.
- Take action on identified gaps. Planning is most effective when followed by clear execution strategies.
The STAR Tool isn’t about finding problems—it’s about creating solutions. By using structured assessments, teams can proactively address concerns and enhance efficiency.
Why Partner with PTAG?
Many organizations recognize the importance of structured shutdown planning but struggle with implementation. That’s where PTAG comes in. Our team of shutdown and turnaround experts brings deep industry experience, proven methodologies, and hands-on support to help organizations:
- Integrate CII Best Practices – We help implement research-backed strategies to improve shutdown performance.
- Optimize Execution Plans – From front-end planning to post-turnaround reviews, we guide teams through every phase.
- Enhance Stakeholder Alignment – Our facilitation services ensure seamless coordination across all disciplines.
- Improve Cost & Schedule Predictability – With data-driven decision-making and structured assessments, we help reduce risk and enhance efficiency.
- Leverage Industry-Leading Tools – We provide expertise in deploying STAR, PDRI, and other critical planning tools.
Our approach isn’t just about avoiding problems—it’s about helping your team execute shutdowns and turnarounds with confidence, efficiency, and long-term success.
How Prepared is Your Team?
If you’re looking to strengthen your shutdown and turnaround processes, PTAG can help integrate best practices for better results.
Reach out to us to learn more about how we can support your team in achieving a more efficient, cost-effective, and predictable turnaround.
Stay tuned for future Hidden Gems webinars, where industry-leading insights for project success will be shared.
Let’s make your next shutdown a success story.